Weld Inspection
Innovating Weld Inspection with TPAC
Weld inspection plays a critical role in ensuring the structural integrity and reliability of critical components across various industries such as manufacturing, oil & gas, aerospace, transportation, and power generation.
The welding process can produce flaws due to the metallurgical changes a material undergoes when exposed to heat or because of inaccurate weld parameters. Defects in welds can compromise the safety, performance, and longevity of structures and equipment, creating a life or environmental risk, making thorough inspection essential.
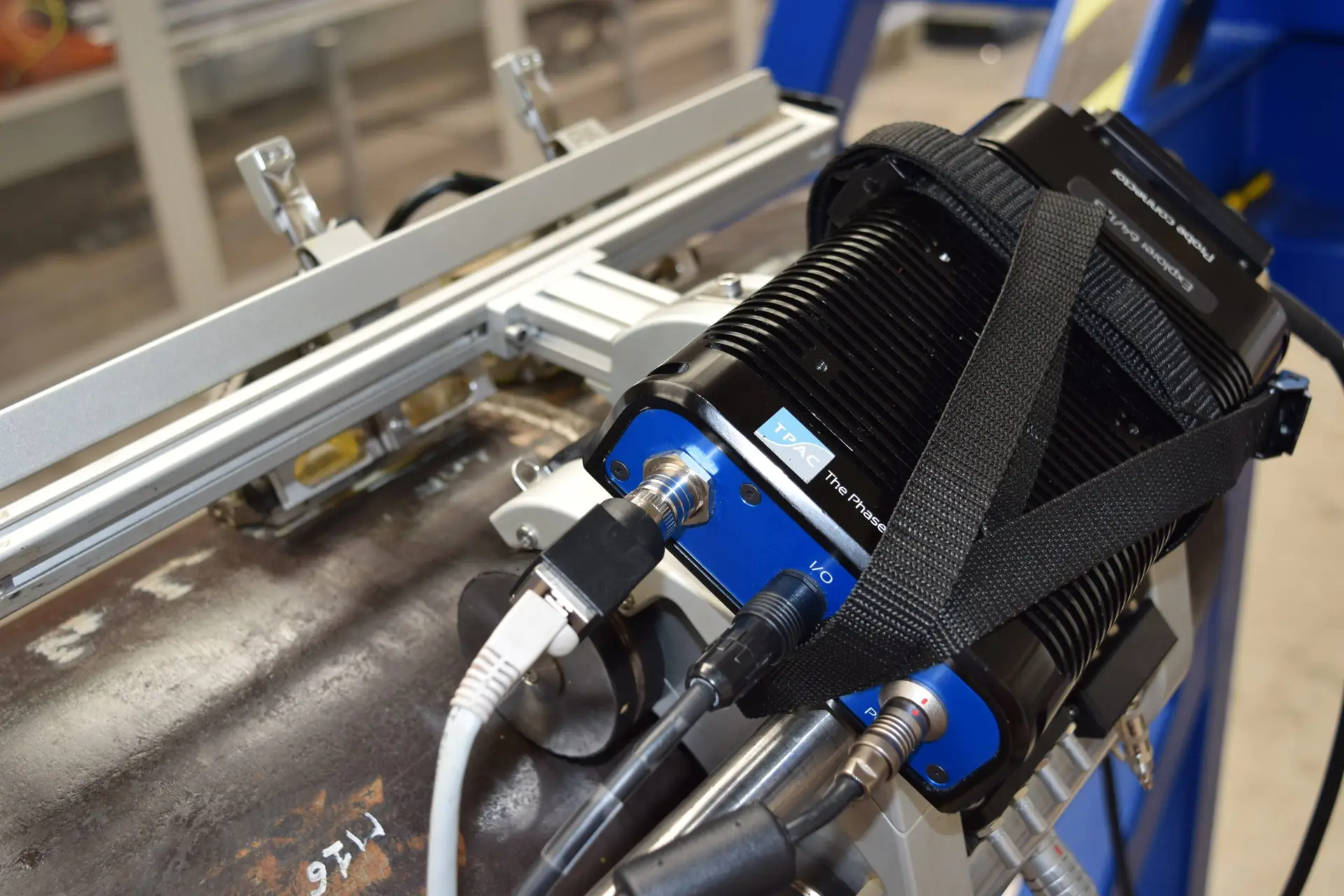
Application of PAUT in Weld Inspection
With a variety on non-destructive testing (NDT) techniques available, ultrasonic inspection (UT) is the preferred method. Within this technique, phased array UT (PAUT) has emerged as a powerful tool, offering several advantages over traditional inspection methods.
By employing multiple advanced tools, PAUT enhances defect detection and characterization while providing real-time feedback, ultimately improving the efficiency and accuracy of weld inspections.
WHAT ADVANCED IMAGING CAN DO FOR WELD INSPECTION
Advanced imaging technologies such as Full Matrix Capture (FMC), Plane Wave Imaging (PWI), Total Focusing Method (TFM) and multiple others greatly improve the detection and sizing of the defects that can be found in weld that include:
cracks, lack of fusion, porosity, incomplete penetration, and slag inclusions.
Better and more accurate sizing allows for less false calls and engineers can apply defect characterization and risk assessment criteria.
The latest technologies such as Adaptive TFM (ATFM) furthers pushed the boundaries of ultrasonic inspection allowing for imaging below the weld cap, an area very difficult or even impossible to reach using other methods.
Paired with Prelude, check how the Explorer Max delivers fast results on the most challenging surfaces in the oil & gas and power generation industries.
TPAC – An advanced selection of ultrasonic acquisition tools
Whether it is for butt welds, fillet welds, and other configurations found in pipelines, pressure vessels, structural components, or more, TPAC offers the tools to successfully inspect even the most challenging welds.
The Explorer, available in configurations ranging from 16/64 to 128/128 and 64/256, provides all the firepower and range you need to address any weldment, from 0.25” to 2” wall thickness carbon steel, austenitic steel, and even CASS (Cast Austenitic Stainless Steel).
Virtually any array configuration is supported; linear, dual linear, dual matrix, or even custom configurations that our software allows you to easily model.
You will enjoy the efficiency and robustness of TPAC’s ready-made inspection software, which is also able to interface with advanced analysis platforms like CIVA or ULTIS.
Is your weld inspection a bit “out of the box”? In that case we have our own Rapid Application Development platform (RAD) that allows us to deliver your inspection software just right for what you need, with no unnecessary tools or menus.
“Girth Weld Scan – Using TPAC’s Explorer on an automated scanner & TWI’s Crystal TM Software.”
Visualizing Weld Defects with TPAC's Advanced Imaging
The following images illustrate the capabilities of TPAC’s technologies:
TPAC: Ensuring the Future of Weld Inspection
With TPAC’s advanced solutions, industries worldwide can achieve a new level of confidence in the integrity of their welds. The company’s commitment to innovation, coupled with its comprehensive portfolio and expert team,
ensures that clients receive not just a product but a partnership dedicated to their success.
This quantitative approach to weld inspection facilitates objective decision-making and enhances quality control processes.