Robotics for Ultrasonic Testing
How are robotics used for ultrasonic testing ?
The growth in use of industrial robotics has provided an interesting new approach to solving ultrasonic testing applications. Robotic applications for ultrasonic testing involve the integration of various robotic systems with UT technology to conduct precise inspections, even in the most challenging environments. The ability for robotic platforms to perform remote inspections in hazardous or hard-to-reach areas without putting human inspectors at risk has improved the overall safety of industrial operations, while often providing an additional benefit of decreased inspection times! Compared to traditional manual inspection methods, robotic ultrasonic testing increases speed, improves efficiency, accuracy, and safety, paving the way for more reliable and cost-effective inspection solutions across diverse industries. Overall, robotics and automation technologies will most certainly play a major role in the future of NDT.
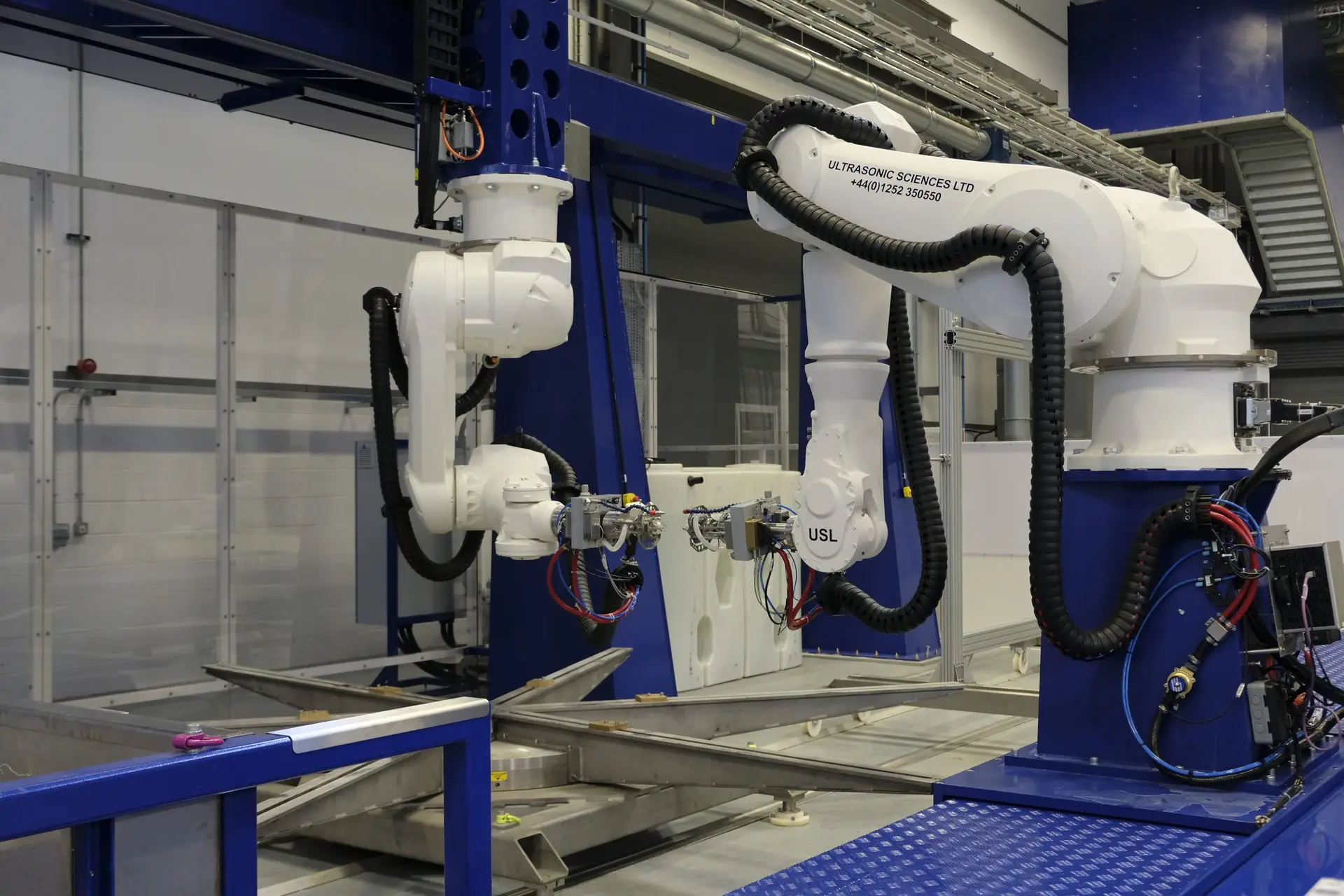
Process
The process involves deploying robotic platforms and systems equipped with ultrasonic acquisition systems and transducers to scan assets, collect data on the asset for real-time or later analysis, and generate comprehensive reports. This innovative approach offers enhanced efficiency, accuracy, and safety, particularly in accessing hazardous or inaccessible areas, making it a valuable tool for experts familiar with ultrasonic testing.
It is often the case that these robotic inspections provide a much more robust ultrasonic data set when compared to historic manual approaches. This provides greater information regarding asset integrity via greater data density, with more ultrasonic measurements of the asset than would have been previously achievable.
AIR COUPLED ULTRASONIC TESTING
Air-coupled ultrasound (ACUT) is an emerging technology within non-destructive testing (NDT) ideal for materials that can’t be exposed to liquid. At TPAC we are excited to introduce our PILOT+, a cutting-edge device set to make a significant impact.
Meet us, and our expert Héctor Calas, at ASNT 2024 for a LIVE demo of Air Coupled Ultrasonic Testing.
Application: Inspection: composites, honeycomb structures, thin metals, and other materials used in aerospace, automotive, and civil engineering.
Detection: Commonly used for detecting defects such as delaminations, voids, cracks, and thickness variations.
Intrigued? Check the article! (3) Air Coupled UT in WCNDT by TPAC | LinkedIn
How Does Robotic Air-Coupled Ultrasonic Testing (ACUT) Work in Practice?
TPAC teamed up with Axiome, a specialist in industrial automation, to present a cutting-edge live demonstration of Air-Coupled Ultrasonic Testing (ACUT) — a fully dry, contactless solution for inspecting composite and mechanical parts.
In this short video, Grégory Charrier, Technical Director at Axiome, explains how our collaborative setup works:
An ABB collaborative robot equipped with TPAC’s Pilot+ device offering 162 dB digital dynamic range — no analog gain required
A fully integrated system for fast, automated, and 100% couplant-free inspections
This solution enables frictionless integration of ultrasonic NDT into robotic lines.
Applications and industries
In industries faced with hazardous environments, whether confined spaces, caustic chemicals, highly flammable conditions, or a combination of all of these, the ability to deploy a robotic platform rather than a human to perform the inspection brings many advantages. Safety is certainly the primary benefit, but many times these inspections can be performed while the asset is still in operation, eliminating lost revenue due to the need to shut down operations to accommodate traditional human-based inspections.
Autonomous or remotely controlled vehicles equipped with ultrasonic sensors for inspecting large-scale infrastructure like pipelines, storage tanks, bridges, dams, and offshore platforms are another important robotic application for ultrasonic testing. These vehicles can traverse challenging terrains or navigate underwater environments, facilitating inspections in otherwise inaccessible areas.
Robotic crawlers outfitted with ultrasonic probes can navigate along pipelines or vessel walls, systematically scanning for defects and anomalies. Used mostly to inspect the integrity of welds in industrial settings.
Another prominent robotic application for ultrasonic testing involves deploying robotic arms equipped with ultrasonic transducers to conduct thorough inspections of complex structures such as those found in the aerospace industry. These robotic arms can maneuver with precision, ensuring comprehensive coverage and accurate data acquisition, while ensuring repeatability of the inspection.
Finally, collaborative robots (cobots) are increasingly working alongside human operators to streamline inspection processes. These cobots are equipped with ultrasonic probes and advanced sensing technologies, allowing for efficient and ergonomic inspection tasks in manufacturing and assembly lines.