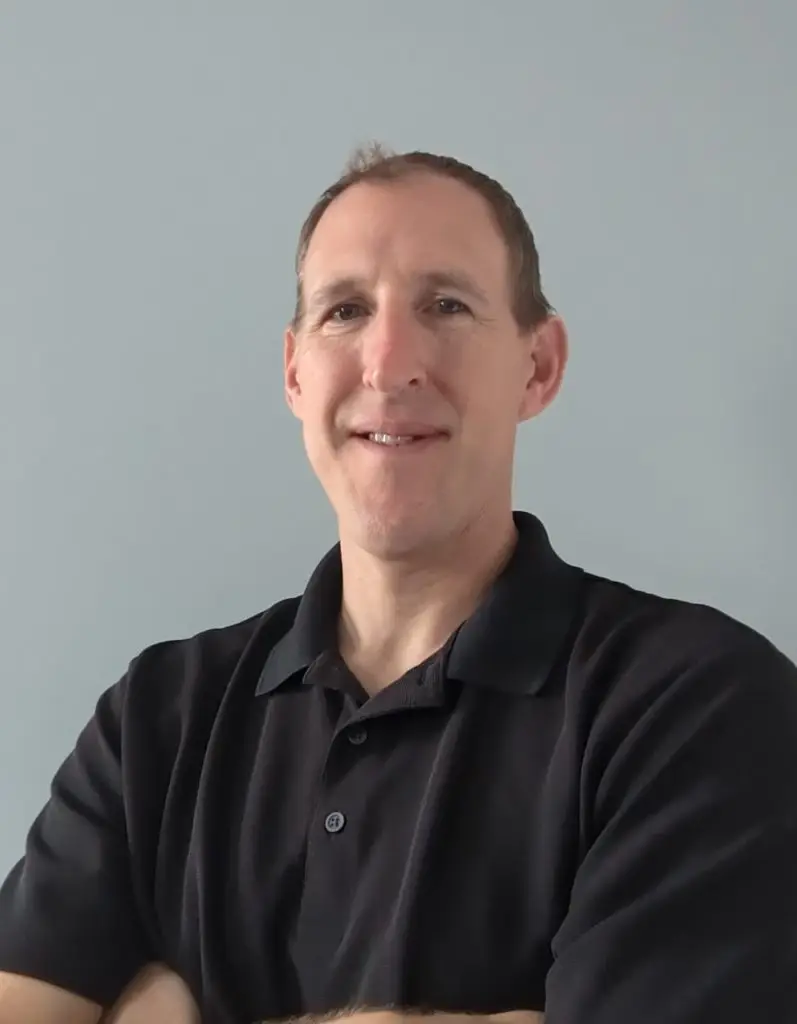
Mike currently works with TPAC’s software and applications teams. He has been in the NDT industry for 25 years and currently holds Level III certification through ASNT in Ultrasonic Testing, Radiographic Testing, Eddy Current Testing, Magnetic Particle Testing, Liquid Penetrant Testing, and Visual Testing.
Mike also holds current API inspection certifications in 510 (Pressure Vessels) 570 (Piping) and 653 (Above Ground Storage Tanks).
Previously Mike worked for Team Industrial Services where he held several roles over the years including Level 3 technician, project manager, operations manager, and most recently as regional SMEs of advanced ultrasonic inspection.
In that role Mike was responsible for technical support of client projects, maintaining the company’s UT procedures, training and certifying technicians, interfacing with clients and providing Level III data review.
We are extremely happy to welcome Mike Sternik in the TPAC team!
What made you drive into Ultrasound NDT world?
While in college I took courses in most of the major NDT methods: MT, PT, VT, ET, UT, RT. After College I took a job working for an NDT service provider as an assistant/helper. Eventually I gained certification in the above mentioned methods and also attained a few certifications through API (American Petroleum Institute). Partially based on company needs, and partially based on skill set I eventually ended up spending the majority of my time exclusively dealing with advanced ultrasonic applications.
Can you share some highlights from your career in Ultrasound NDT?
Early on in my UT career I was lucky enough to be put in a position to learn from more senior technicians.
I was also provided the opportunity to professionally advance by attending multiple UT training courses which made a big impact on my career path.
As my career advanced, I was eventually put in a position to supervise others. That provided its own set of challenges but I found it to be a very positive experience.
Concerto : showing Inclusions/Laminations with PWI
What are some of the most challenging projects you've worked on?
I’ve been involved in a lot of interesting projects over my career. Some of the more significant ones include taking part in developing inspection techniques to be implemented in an asset owner’s in-service inspection program, developing guided wave procedures and techniques for inspection of process piping, and developing procedures and techniques for inspecting high energy piping for in-service damage.
What are your preferred techniques or methods in Ultrasound NDT?
In-Service Inspections
I find in-service inspections to be more interesting than inspections in production environments. In-Service cracks can occur in any orientation, in any direction, and be of any size from microscopic to massive. That keeps you on your toes. Also, once indications are detected, then an investigation usually begins to determine both the indication cause, and how detrimental it is to the service life of the component. This generally involves doing a deep dive into the asset’s inspection history, and reviewing the expected damage mechanisms based on the service history. This is usually followed up by collaboration with experts from multiple disciplines to determine a path forward including FFS engineers, process engineers, and metallurgists among others.
Stainless Steel /Coarse Grained Weld Inspections
Coarse grained welds present unique challenges not found in typical carbon and low alloy welds. Standard shear wave techniques of coarse grained welds typically need to be modified to include supplemental techniques such as refracted longitudinal waves to properly evaluate the as-welded portion of the material. I find it much more interesting to work on complex grain structure materials than standard carbon steel.
How do you stay updated with the latest advancements in the field?
First and foremost listening to customers. All customers have pain points, such as equipment that is difficult to inspect, and/or equipment which is susceptible to damage mechanisms which don’t easily lend themselves to detection with standard NDT methods. Once the problems have been identified, then the search for solutions can begin. The first step primarily involves doing some research to identify the current inspection techniques and where they fall short. The next step may involve reaching out to equipment manufactures to develop custom solutions. That’s how I originally discovered TPAC.
Through a combination of hardware and software they were able to provide a unique solution for detection of a historically very difficult type of crack to detect in the power generation industry.
Prelude : showing a welded plate with manufactured flaws with TFM
What trends do you see shaping the future of Ultrasound NDT?
AI
I know it’s a buzzword everyone likes to use, but I don’t believe most people in the NDT industry have fully considered its long term implications. From the multitude of studies done on POD (Probability of Detection) it’s clear that there is a wide range of skill level among Level 2 inspectors (and even good ones have bad days). I believe AI, initially in the form of assisted analysis, and long term in the form of full analysis has the potential to provide asset Owners with a much higher degree of confidence that a particular inspection will adequately identify and characterize the indications necessary to make an informed decision on the continued service of the component.
High Temperature UT Inspections
Asset owners are constantly searching for ways to both extend the life of aging equipment and to properly budget and plan for equipment replacement.
The term “discovery work” is a common term used in industry for inspections which must be performed during shutdown. To that end, on-stream high temperature UT inspections have the ability to not only reduce the amount of unexpected shutdown discoveries, but also monitor existing indications from a Fit-For-Services perspective. Because of this they are increasingly playing a more significant role in inspection programs.
What do you believe are the key elements of successful teamwork in NDT projects?
Listening. When to listen and when to speak is one of the hardest skills to master. Everyone has a unique perspective and skill set. From the welder, to the pipe fitter, to the software programmer. Absorbing information from everyone involved in the project, especially when it’s in someones area of expertise, is critical to the success of any project.
Are there any specific areas within Ultrasound NDT you are passionate about?
It’s been interesting to see how the UT industry has advanced over the past 20-25 years of my career. I’ve watched the transition from high temperature PAUT not being possible, to 300F-400F being a run of the mill inspection.
I’ve also taken part in the evolution of PAUT of coarse-grained welds.
Currently I’m most interested in FMC, specifically from the perspective of understanding how existing and new reconstruction algorithms may be used to improve current inspection techniques
Prelude : ATFM LL on top of a weld picking up a slag pocket
How do you balance your work and personal life, especially in a demanding industry like NDT?
Throughout my career I’ve often had to work odd hours, and had some degree of travel. It can be difficult balancing travel or long hours with home life, but at the same I think I’d be bored if I was in a typical day job. But, in the end, it’s the field I’ve chosen. Vessels and pipes don’t only explode Monday through Friday between 9am and 5pm.
What attracted you to join TPAC and what are your goals for the next few years?
What attracted me to TPAC was their reputation for being a global leader in the development of advanced ultrasonic equipment and software. I also had a very positive firsthand experience collaborating with them in the past. TPAC’s current organizational structure also provides a unique opportunity for each employee to have a significant impact on the future direction of the company.
How can readers and potential clients connect with your team for further inquiries or collaborations?
We have colleagues in many places around the world (USA, Europe, Asia). You can contact us through our website. Personally, I can be reached on LinkedIn and ResearchGate or by e-mail.
What are some resources, events, or publications where readers can stay updated on the latest developments in ultrasonic testing?
For research topics, I personally read a lot of articles, in particular in NDT&E International or IEEE TUFFC. I also like the IEEE IUS conference which has a great scientific level. Our team also goes to many conferences like ASNT, AMPP, PPIM, ECNDT, and WCNDT etc.