Composite Inspection
What is Composite Inspection?
Composite materials have transformed a wide range of industries and applications for their unique characteristics, often superior to those of their individual constituents, which make them desirable for a wide range of applications in aerospace, oil&gas, automotive, construction, marine, and sports equipment. These materials include Carbon Fiber Reinforced Polymers (CFRP), Glass Fiber Reinforced Polymers (CFRP), Metal Matrix Composites (MMC), and Ceramic Matrix Composites (CMC).
The composite manufacturing processes and technologies involved keep evolving nowadays, and the benefits are multiple and diverse: production costs, design flexibility, resistance to corrosion and wear, strength-to-weight ratio, stiffness, flexibility, thermal stability, etc.
The unique structure of composite materials, sometimes anisotropic, also result in specific defects potentially generated during their production or operation, which should be detected on time to assure their integrity in safety critical applications. Those defects include delamination, porosity, fiber misalignment, wrinkle, moisture ingress and multilayer disbond.
Ultrasonic Testing (UT) is one of the main NDT methods used for this purpose, and TPAC provides a set of top-notch technologies and solutions able to meet the most demanding requirements in composite inspection, including those related to high-attenuative materials (as thick honeycomb-CFRP sandwich-structures), dry inspections (using air-coupled UT), and complex shapes.
Process
Composite inspection is a mandatory step within the quality control of many industries. The most common UT techniques are pulse-echo (PE) for low-attenuation materials, and Through-Transmission Ultrasound (TTU) for high-attenuation materials.
In addition, TPAC has developed unique features to solve the most challenging composite inspections, using state of the art TFM and PWI methods, dealing with some critical characteristics of these materials such as anisotropy, complex/irregular shape, or high ultrasonic attenuation.
On top of this, the robotization of composite inspections has created new challenges, beyond what portable and laboratory instruments are designed for. Compactness, high-performance, robustness, and synchronization with robots are the most important factors.
TPAC has developed cutting-edge technologies to meet these requirements, making possible the integration of high-performance instruments (up to 20 Gb) very close to the UT probes, which makes a big difference in the signal quality and allows for a variety of UT techniques (including TTU, PAUT, TFM and PWI) in multiple robotic configurations (including single- and twin-robots, immersion tanks, flatbed scanners, and Cartesian gantries).
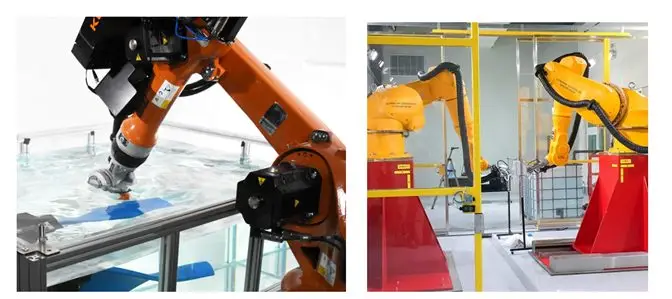
TPAC instrumentation integrated in a variety of aerospace robotic inspection systems
Applications and industries
Composite materials are utilized across a wide range of industries due to their unique properties and benefits.
Some of the industries that commonly use composite materials include:
Standards and R&D
TPAC takes actions to study new technologies and participate in steering committees that promote these innovationsAirworthiness & deviation
Benefit from the latest innovation for fast containment situation and connection actionsMRO
Reduce aircraft downtime and inspection cycles with dedicated easy to apply solutionsComposite
Insprection of anisotropic and attenuative structures, complex materials and complex shaped partsElaboration, forging, machining
Support for statistical process controls and quality check solutions for manufacturingAerospace
Composite materials are extensively used in space and aviation applications due to their high strength-to-weight ratio, corrosion resistance, and design flexibility. For instance, they are used in aircraft components such as fuselages, wings, empennages, fairings, engine turbine blades, and interior structures.
Automotive
The automotive industry utilizes composite materials to reduce vehicle weight, improve fuel efficiency, and enhance performance. Composites are used in components such as body panels, chassis, interiors, and structural reinforcements.
Marine
Composite materials are widely used in the marine industry due to their resistance to corrosion and fatigue, as well as their lightweight properties. They are used in boat hulls, decks, masts, and other marine structures.
Wind Energy
Composite materials play a critical role in wind turbine blades due to their strength, stiffness, and fatigue resistance. They enable larger blade sizes, which increase energy capture and efficiency in wind power generation.
Construction
Composite materials are increasingly used in construction for their durability, weather resistance, and design flexibility. They are used in applications such as bridges, building facades, cladding, reinforcement bars, and infrastructure components.
Sports and Recreation
Composite materials are widely used in sports equipment such as tennis rackets, golf clubs, bicycles, hockey sticks, skis, and snowboards due to their lightweight and high-performance characteristics.
Military and Defense
Composite materials are utilized in military and defense applications for their strength, lightweight properties, and resistance to corrosion and impact. They are used in components such as armored vehicles, body armor, aircraft structures, and radomes.
Renewable Energy
Apart from wind energy, composite materials are also used in other renewable energy applications such as solar panels and hydroelectric turbines, where their durability and resistance to environmental factors are advantageous.
Electronics
Composite materials are increasingly used in electronic devices and consumer electronics for their lightweight properties and electrical insulation capabilities.
Oil&Gas
Composite materials are becoming a substitute for many metallic components used in petrochemical applications mostly for their excellent corrosion resistance and mechanical properties.
These are just a few examples, but composite materials find applications in many other industries as well, demonstrating their versatility and importance in modern manufacturing and technology.
Our solution for corrosion mapping?
TPAC provides a complete solution to best assess the potential corrosion without causing damage to the materials or structures you need to inspect.
Pair the Explorer device that best suits your needs with our software designed for corrosion mapping, Concerto! And you are all set!
High-Dynamic Range TTU
When it comes to the inspection of high attenuation materials, like most honeycomb sandwich aerospace components are, ultrasound inspection must be done in the so-called Through-Transmission Ultrasound (TTU) mode. Ultrasound transmission across these materials demand high enough dynamic range instrumentation, not only to penetrate them, but to be able to inspect thinner or less attenuating areas in the same part or batch without changing gain or other setting.
To answer this and other requirements, TPAC has developed Pilot +, a unique instrument for doing ultra-high dynamic range (162 dB acquired at once) and high-resolution (27 bits) acquisitions, everything in an ultra-compact IP-67 housing, making unnecessary to worry anymore about the gain setting.
Pilot + is integrated into a compact IP67 housing and features:
- 8 UT parallel channels for doing pulse-echo, pitch & catch and TTU
- Broadband bandwidth receivers (50 kHz…20 MHz) allowing low frequency techniques as Air-Coupled UT
- Powerful (up to 400 V) and versatile pulsers with different modes available (unipolar, bipolar-burst, and Arbitrary-Wave Generation or AWG)
Arbitrary Wave Generation
TPAC Arbitrary Wave Generation (AWG) is becoming another game-changer in composite inspection.
The capability to create and process arbitrary signals (as compared to the traditional spike or square wave pulsers), has open an exciting field of possibilities to further improve SNR and resolution by better matching the acoustics between the ultrasonic instrument and the probe and material under inspection.
AWG technology is available in the high-end instrumentation from TPAC, both in Phased-Array and conventional UT instrumentation: Pioneer, Explorer MAX, and Pilot.
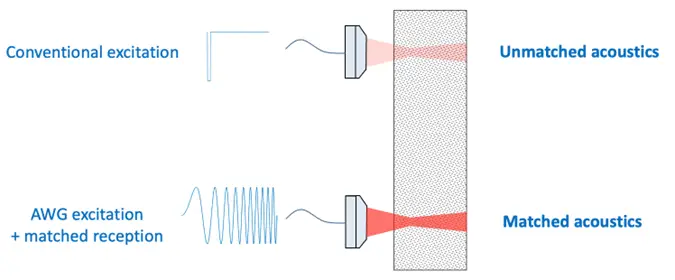
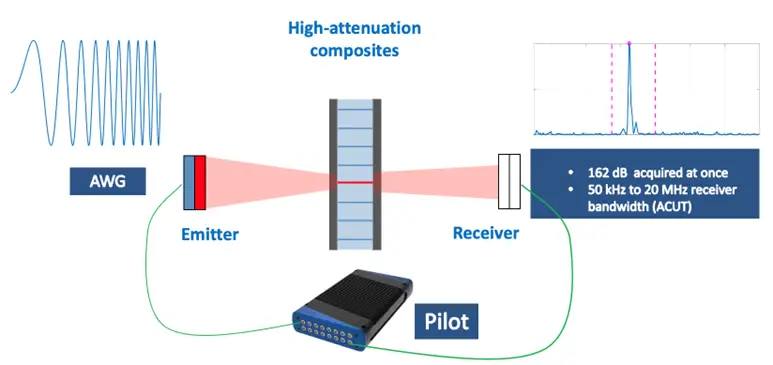
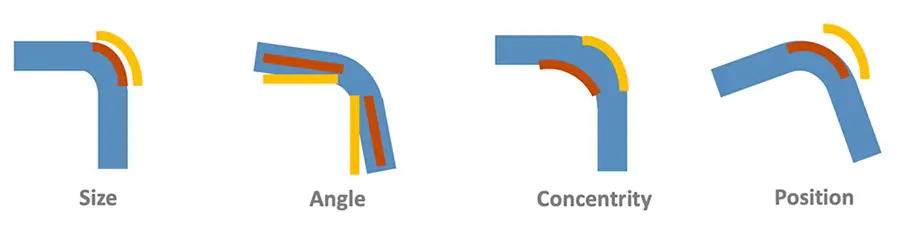
Typical variations of radii in CFRP aerospace parts
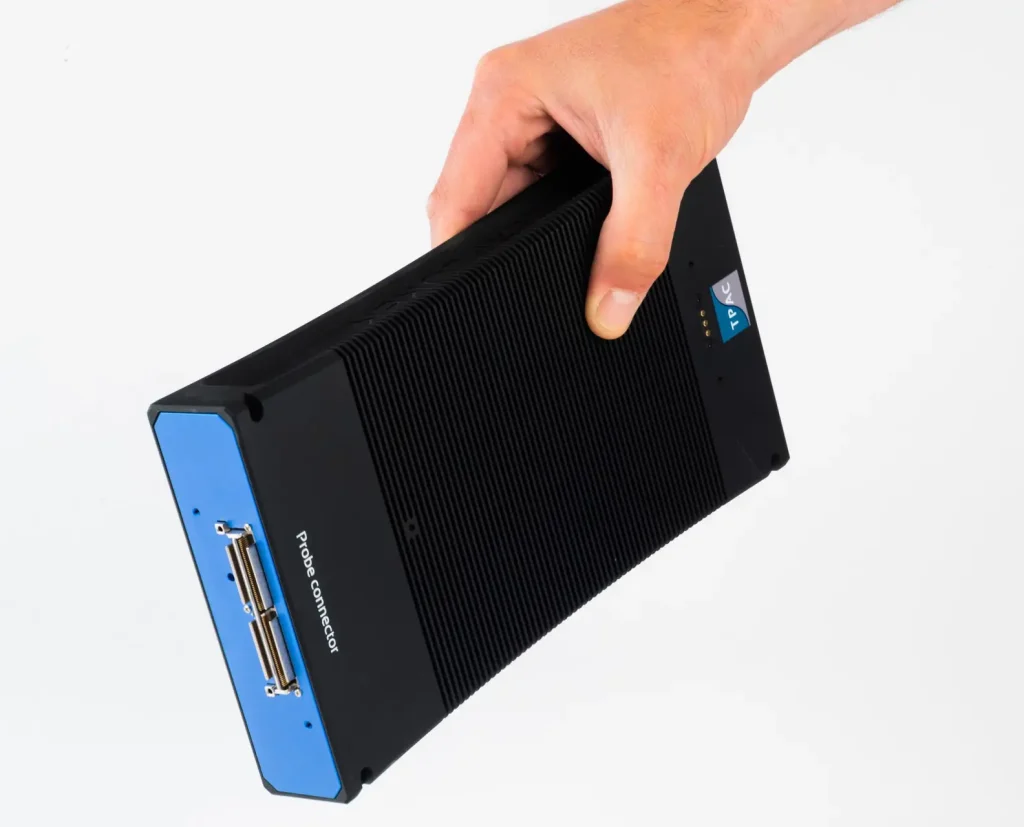
TPAC Explorer MAX, ultra-high-performance (10 GbE)
compact phased-array instrument
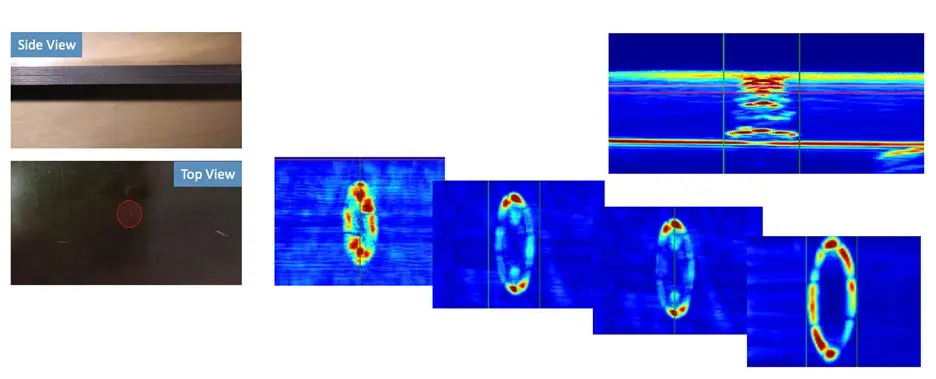
Impact damage scan on a CFRP monolithic plate by APWI, showing lateral and top views at different depths (B-Scan and C-Scan, respectively)
Adaptive TFM/PWI
TPAC has developed unique Adaptive TFM/PWI methods to overcome the challenges derived from complex geometries, variable thickness/curvature, or irregular shape very common in composite inspection.
A typical application is found in the aerospace production of CFRP components, frequently designed with radial geometries which are prone to small dimensional deviations in the manufacturing phase, normally not relevant for their structural mission, but very significant in the ultrasonic coupling, provoking uncontrolled attenuations that could be confused with false porosity indications or even make the own UT inspection unfeasible.
Also, the latest advances in 3D printing (Additive Manufacturing or AM) are allowing the generation of composite parts with complex shapes, previously difficult or impossible to produce.
Real-time ATFM/APWI imaging becomes now possible with the high-end full-parallel phased-array instrumentation from TPAC, like Explorer MAX. Adaptive imaging is also applicable to other TFM variants as PWI and PCI (Phase-Coherence Imaging).
In ATFM/APWI not everything about complex shapes: one the main applications is correcting probe-to-surface misalignments, either in manual, semi-automatic, or automatic inspection (profile-following), solving the “last mile” in terms of ultrasonic coupling and accuracy, relaxing in this way the mechanical requirements, what is of great help in the inspection of CPRP components, even when their geometry is flat or quasi-flat.
Benefits
TPAC has developed cutting-edge technologies (hardware and software) which are solving and improving a wide variety of existing applications in Aerospace and enabling new ones, collaborating with the main system integrators and OEMs in many industries like aerospace or power gen, to provide top-notch UT inspection solutions.
Compactness, robustness, and performance are common factors in the TPAC portfolio, which makes a big difference when it comes to the integration with robots and to the inspection of complex and highly attenuating components.
In summary, TPAC instruments play a critical role in ensuring the safety, reliability, and performance of composite materials across various industries. By leveraging advanced ultrasonic techniques and instrumentation, manufacturers can detect defects early, optimize production processes, and deliver high-quality products to meet the demands of modern engineering challenges. Whether in aerospace, automotive, marine, or renewable energy applications, ultrasonic inspection continues to be indispensable in the quest for excellence and innovation in composite materials.